中国造船行业真相:跟日韩竟然还有20年差距?
设计开发能力不足。自改革开放以来,中国先后引进100多项船舶和船用设备设计制造技术,但多数造船企业并未重视对引进技术的消化吸收和自主创新,中国船型设计开发能力仍显不足。
设计技术落后。船舶设计软件大多依赖国外引进,造船核心技术的知识产权归属国外造船强国;自主设计船舶往往用钢量偏高,经济指标偏低,生产设计深化程度约为发达国家的50%~60%,设计差错率则远远高于发达国家。在所造船舶中,自主开发产品不多,大多船舶的原始设计来自国外,特别在高新技术船舶方面,仍未摆脱依赖船东或国外设计院所的被动局面。
船型开发薄弱。由于核心技术缺乏和对技术创新能力建设的不足,不少造船企业技术力量主要为应付生产任务,处于"先合同后设计,边设计边建造"和"来料加工"的被动局面,极少技术储备和技术开发。已开发的内河标准船型,主要考虑船闸通过率,而对航道水深利用率、码头岸线使用率和船舶载货量考虑较少,船东造船热情不高。
自主设计萎缩。能够自主设计和开发建造国际船舶16大类中的6类,有8类能够建造但只能购买设计。一些民营造船企业根本未设设计开发部门,靠拿他人的设计图造船,市场适应力更差。
精度控制技术薄弱。目前,日韩造船企业几乎达到分段100%无余量上船台,除艉柱分段外,所有分段精度控制成功率为80%~95%,大合拢间隙基本控制在5±3mm,最大为12mm。中国在精度控制技术方面与先进造船国相比,存在一定差距,部分造船企业分段造船大合拢间隙有时高达20~50mm。专家评价,中国造船企业在精度造船和综合管理水平方面要比日韩造船企业落后10年以上。
在造船模式方面,中国造船行业的整体水平大致处于国外上世纪90年代中期水平,由传统的"分段制造"向"分道建造"过渡阶段,而日韩造船企业已经处于壳舾涂一体化的"集成制造"阶段。在钢材利用率方面,日韩等国造船企业对原材料的利用率超过90%,中国为85%~88%。在区域涂装技术方面,中国船舶涂装工时消耗率为0.85h/m2,日本则为0.25h /m2,油漆材料消耗是日本的1.24倍。在区域舾装技术方面,日韩的预舾装率已达95%左右,中国只有70%。
造船生产效率低下。中国造船行业生产效率大大低于发达国家。有资料表明,造船行业生产效率约为发达国家的1/7~1/10,若按人均产值或人均产量对比,仅为发达国家的1/20或更低些。有研究资料指出,目前9家大型造船企业的造船水平与国外的差距约为14年。在人均年造船吨位、人均年产值和生产效率3项指标上,造船企业与国外先进造船企业相差5~7倍。据测算,如果日本生产效率为1,韩国为2/3,中国则只有1/7~1/5。中国在分段建造过程中尚未做到跟踪补涂,分段二次除锈比例达60%~80%,甚至达100%,涂料消耗系数达1.9~2.0。而日韩造船企业普遍采用机械化钢板预处理、分段制造过程中跟踪补涂方式,分段二次除绣面积在20%以下,涂料消耗系数仅为1.2~1.5。中国造船企业的大量浪费、重复施工和返工,使工时浪费达55%,实际工时约为日本造船企业的8~10倍。
信息集成技术欠缺。上世纪90年代中期,日本大型造船企业在推进计算机集成制造技术的实体化应用上取得重要进展,节省人工50%,缩短工期20%。韩国造船行业采用TRIBON系统,使设计周期缩短25%,建造周期缩短10%。中国造船行业自上世纪80年代初开始实施CASIS、CADIS、CMI-S的3C工程,为中国造船行业在信息化建设中打下技术和思想基础。但由于条件限制和发展局限性,中国信息集成技术方面存在如下问题。
缺乏标准体系。技术、管理和工作标准体系的缺乏,造成各造船企业制定的实用标准有局限性,影响企业信息化的建设发展。
设计与生产脱节。设计院所和造船企业的脱节以及传统习惯的影响,造成诸多重复劳动和错误的出现,并行协调(设计院所与造船企业,造船企业内部生产部门之间)不够顺畅,生产效率和产品质量跟不上形势要求。
代码和接口标准不统一。代码不统一造成行业内部、企业之间和企业内部在信息化建设中资源共享困难。接口标准不统一使信息数据重复输入,数据错误率上升,降低信息资源的利用率,出现资源浪费和信息"孤岛"。
仿真技术研究和应用深度不够。难以将分散在大量设计图上的二维信息汇总成三维图像系统;无法实现利用计算机进行设计信息验证、开发高精密度的产品以及从构件自动展开到用于船体材料切割的参数自动输出等高效流畅的信息一体化;无法满足对船舶结构、管系、舾装、电力布置、虚拟仿真、生产计划、设备采购进行集成和简化的要求。
配套设备认知度低。长期以来,中国在船用设备领域研发投入严重不足,船舶配套业总体技术水平严重滞后;船用核心部件大部分需要依赖从国外进口解决;部分产能是授权许可证生产,产量满足不了需求;自行设计制造的部分船用设备产品品牌认知度很低,无法在世界范围内享受维修等配套服务,从而得不到国际船东的认可,只能为沿海小型船舶和内河船舶配套。据统计,中国造船行业配套设备本土化率平均不到40%,其中,万吨级轮船的柴油机本土化率不到20%;重要电子系统的本土化率不到17%。而日本造船行业配套设备本土化率达98%~100%,韩国超过90%。
目前,国际海事新规频繁出台,产品升级换代迫在眉睫,国际上绿色环保、节能减排、安全可靠、智能化和集成化的船舶及海工配套产品不断出现,更新换代速度明显加快,对船舶配套技术提出了更高要求。中国众多造船企业基本上是"组装厂",船舶配套业自主研发能力薄弱,船舶关键设备和系统长期依赖引进。日韩和欧盟等加大技术研发力度的同时,加强对中国技术封锁,为占领船舶配套市场采取低价竞争策略,给处于不利地位的中国船舶配套业带来严峻挑战。
生产管理方式落后。中国大部分造船企业基本上还是沿用计划经济体制下的传统管理模式,在管理信息化方面没有从管理理念、组织模型和业务流程等根本问题上进行改造,而仅仅是在原有管理方法下采用信息技术手段。先进的造船技术要求船舶的基本设计、船体结构设计、舾装工程设计、全船和区域的综合布置设计,三维立体模型的共用数据库和各车间的生产信息等都实现计算机化,达到制造过程的标准化和模块化,自动化和半自动焊接技术几乎覆盖所有焊接作业。中国造船企业在生产管理、物料需求和供应管理、资源计划和生产成本控制等方面远远落后于现代造船行业的发展要求。 每一个船人估计心里都清楚是什么水平,表面上的第一大国,实际上南北船下面能把三大主力造明白的也没几家吧。
设计大多靠买靠仿靠偷,像上船院这种号称全国前三的设计院出来的图纸基本每次都是各种洞,一不小心船厂就得百万扔进去填,行业低迷导致新生力量严重不足,稍微强一点的学校应届生基本待不了两三年就走了,两化融合喊的震天响,然而就船厂的工资水平能招来什么水平的IT人员呢?当然设计上还算好一点,毕竟这么多年下来还有一些老师傅在,经验可以传承下来。建造其实才是我国船舶行业最无奈的地方,行业低迷将近10年,明显感觉现场施工水平江河日下,很多老师傅都不来干船了,毕竟船上大多数活有了手艺去陆地一样干,外包队水平一年不如一年。船厂现场管理仍然和以前一样粗放,不说国外,跟南通川崎差距起码就有10年了吧,每年都转模转模,报告出了一堆最后现场还是那么干。
产业升级最根本还是靠从业人员平均素质的提高,几艘邮轮造出去不过是另一场科技大跃进,这种不计成本的卫星放出去既不能形成产业链去剪外国羊毛,又不能改善设计能力根本上的不足,到最后还是每次空船跑出去油耗总是比别人高。
船舶行业是个周期行业,就目前船龄和需求看,离下一轮行情起码还有5-10年,这段时间虽然困难但是却真的是个机会,如果能够大规模采用机器人,从而弥补建造水平差距,减少劳动成本,提高技术人员待遇,这个行业才会有点希望吧。其实船舶和航天也是异曲同工,一方面靠着科研所在军工上成果丰厚,一方面靠着偶尔放个大新闻在民用上维持面子。外行看热闹,内行看门道,工资条拿出来一看,有没有发展各位船人应该比我清楚得多。
那个所谓的超级工程LNG,我这么跟你说吧,专利,钢板,焊材,大大小小的设备,甚至就连第三方检验,都是国外的。中国就是出了人和场地。
真有这么可怕吗?现场工人会告诉你松下的电焊机比上海施威的耐操;日本船级社验船师送给工人的锤子比国产的做工精细;劳氏的验船师从韩国进口的钢印就算化学成分跟中国的一样但是人家的就是坚硬无比怎么敲都不会劈更不会在上面出来一朵蘑菇。
我还真就不是妄自菲薄悲观厌世。
因为当你面对的德国工程师跟你说,我的救生艇艇架可以用静载荷做冲击载荷;当康世博一套软件卖你种100年地才能换来的钱你不买还不行因为别家没卖的好吧其实有另外一家是劳斯莱斯;当全世界的船用主机基本用的都是瓦锡兰或者曼恩的牌照;当中国船级社大放异彩说自己已经有28个挂旗国授权然后某船级社不屑的说我们145个的时候,你会发现,落后确实不可怕,可怕的是,自己明知自己落后却意淫取得的小成绩,无视别人的更大的进步。本来就差了10年了,你用走的怎么去追人家跑的?
我承认你说的那些都是进步,可是那是跟你自己的几十年前比,你看到这几十年里,人家做了些什么了吗?
多说无益,多般一块砖比这些争论更有意义,起码对我来说是这样。
当年还有一个液化石油气船的项目,钢板日本进口。为什么要进口呢?因为机械性能指标的特殊性,宝钢的钢板要加镍,而日本仅仅通过轧制工艺的改进,在不添加镍的情况下达到了同样的机械性能。学材料的人都知道,高强度钢的脆性是致命的,可是他们的钢板在零下60度做冲击试验,吸收能指标甚至好于我们加了镍的钢板,所以导致价格方面进口的比国产的还便宜。
在焊接方面,第一批焊材韩国进口,见证试板合格率基本不会低于95%。后来为了节约成本,换成了昆山一家的产品,紧接着就是一个礼拜做坏了四块,这意味着整整200米做过100%射线探伤的焊缝全部要批掉重新烧焊。得不偿失对不对?
这才是我最害怕的。
而五年前,日本就能用铸造法制作大型发动机的曲轴了。铸件比锻件便宜多少,大家心里都有数吧?
这些都是活生生的例子,我自己亲身经历的。我参与了LNG的项目,我参与了液化石油气船的项目,我亲眼看到了那个铸造的曲轴。
中国造船界和日韩的比较
造船效率上,每修正总吨(可以简单理解为载重吨),中国需要23~30个工时,韩国需要17个工时,日本仅需要8.1个工时。
管理上,中国船厂的计划是自上而下的,日本船厂确是由下而上的提计划,领导只负责指方向。(引自转模学习材料,不是我的一手资料)
设计重量上,低端的货船,日本较中国设计轻约5%~10%,举例来说,20万吨散货船,空船重量3万吨左右,目前价格约3.2亿人民币,日本可以较中国轻2000吨,大约成本较中国船厂少2000万人民币,约6%。这仅仅是结构重量上的差距,设备选型和工艺上的差距更大。
船舶配套钢材方面,目前我国的特种钢行业只能说刚刚兴起吧,比如船用不锈钢和5镍钢、9镍钢,主要靠进口,LPG和罐式LNG船的主要设计公司GTE公司要求所有的国产液罐必须进口钢材。常规的钢材倒是自给自足无虞。
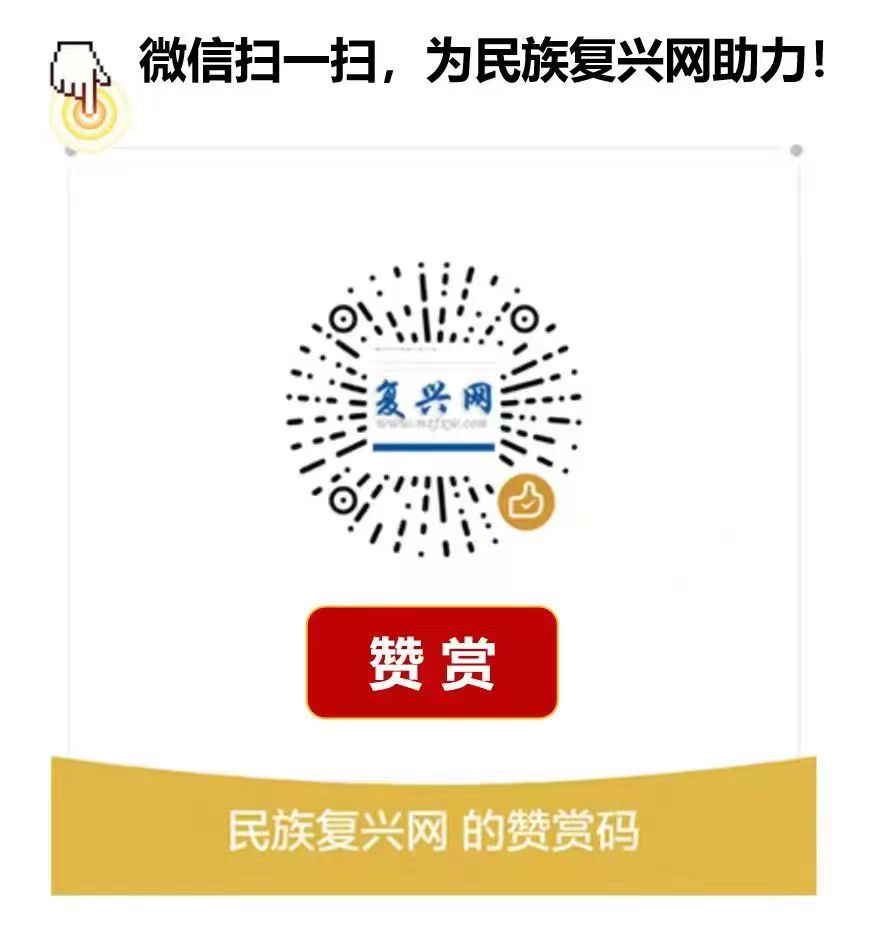
微信扫一扫,为民族复兴网助力!
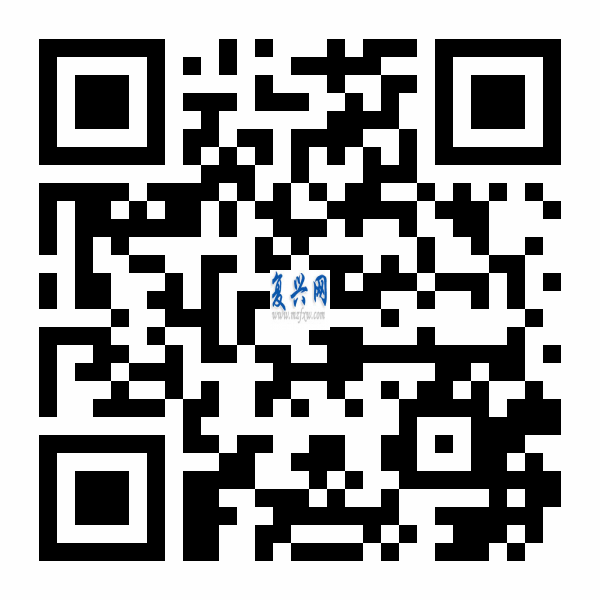
微信扫一扫,进入读者交流群
网友评论
共有条评论(查看)